N-MES
Manufacturing Execution System
A system that shares real-time production site information from the shop floor to the management level.
Digital Transformation
Directly or indirectly collects and aggregates production information that occurs minute by minute at the production site through 4M (materials, equipment, work methods, and workers), and processes the information in real time. It provides a system environment where information can be shared.
A system that shares real-time production site information from the shop floor to the management level.
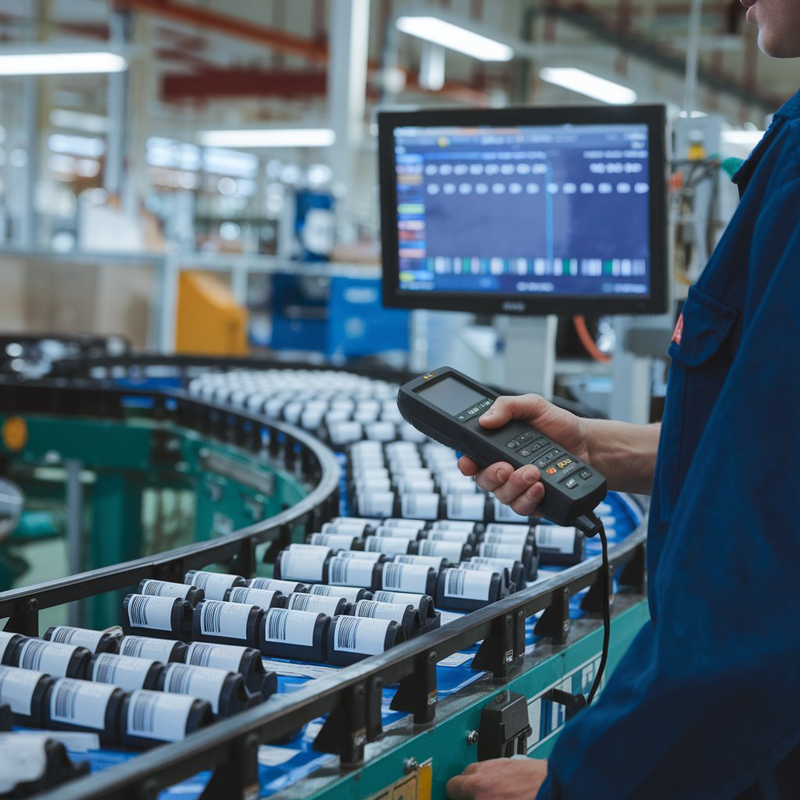

Integrated Operations Management
Enhances operational efficiency by providing more useful and systematic production data from the shop floor through the network, which formalizes the process.

Real-Time Monitoring
Provides a system that enables the acquisition of intuitive information for the efficient management of resources, while collecting and analyzing relevant data to serve as a basis for quality activities.

Barcode-Based Management
By using barcode readers at the production site to collect data, the system prevents input errors and omissions that may occur with manual key-in processes, thereby enhancing data accuracy and ensuring ease and speed of information acquisition.
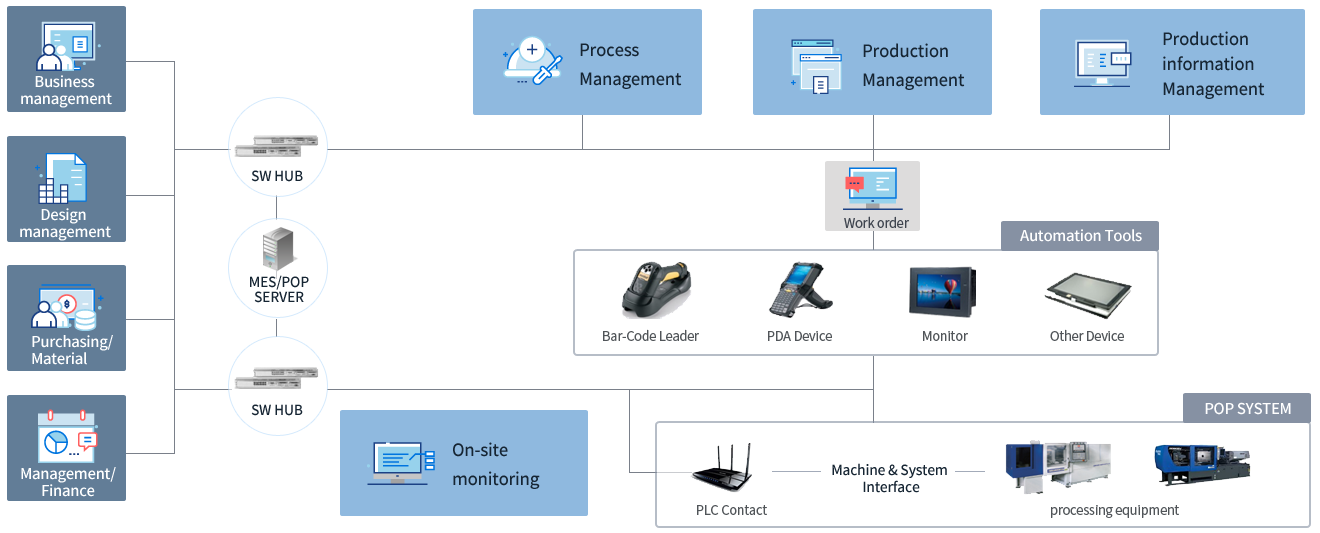
System Features and Advantages
Qualitative effects such as production lead time reduction, production lead time reduction, quality improvement, etc
Introduction of advanced systems
- Optimal design based on lightweight application framework optimized for manufacturing execution systems
- Easy-to-expand structure with intermodule dependencies removed
- 365 days * 24/7 non-stop system oriented and offers a variety of OS environments
Establishment of performance management system
- Systematic management of production activities is essential, and data generated during the production process is analyzed to eliminate unnecessary elements and reduce production costs
- Reduce defect rates and increase profits by changing production conditions and quickly solving problems during production
Increase Analytical & Improvement
- Real-time monitoring of production sites should be possible, and defect rates should be reduced by changing production conditions through rapid information delivery between managers and workers and quickly solving problems during production
- Improves productivity by enabling early prediction of inefficient, inefficient factors within an organization and improving them
Securing manufacturing competitiveness
- Improve quality, such as reduction of malfunction or defect in production site
- Real-time tracking and management of production activities
- Establishment of production plan distribution method and import system
- Accelerate information acquisition to reduce costs and collect product cost information
Improve management standards through business standardization
- Establishment of work process by introducing NMES
- Establishment of a reference information management system (ERP linkage)
- Establishment of accurate work instruction and production system
- Drive production processes and functional improvements by reducing worthless factors
Quick and flexible manufacturing site response
- Provide up-to-date on-site information
- Differences in actual inventory status by process can reduce inventory reserves and identify detailed inventory
- Efficient facility management through facility operation, inactivity, failure information aggregation/analysis
- Respond to emergency orders through real-time process monitoring and re-working inventory
Data Collection Method
System Facility Information Acquisition Guide
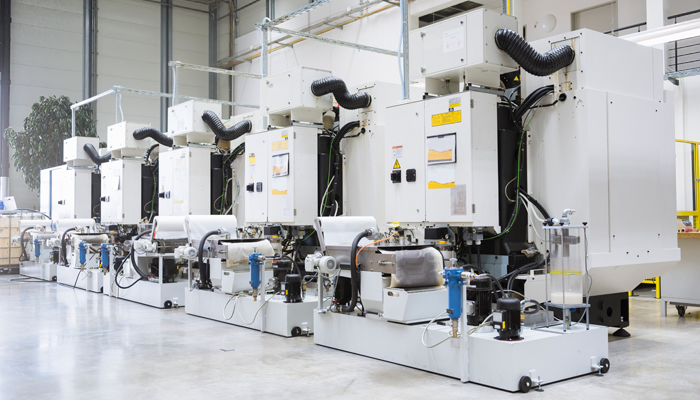
production facilities/PLC
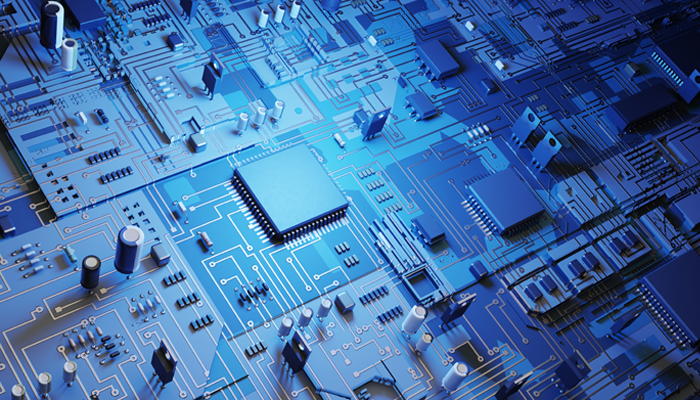
Digital Input/Output Module
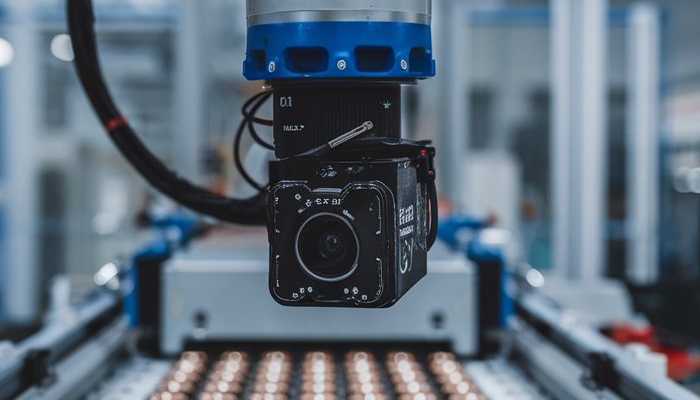
Vision equipment
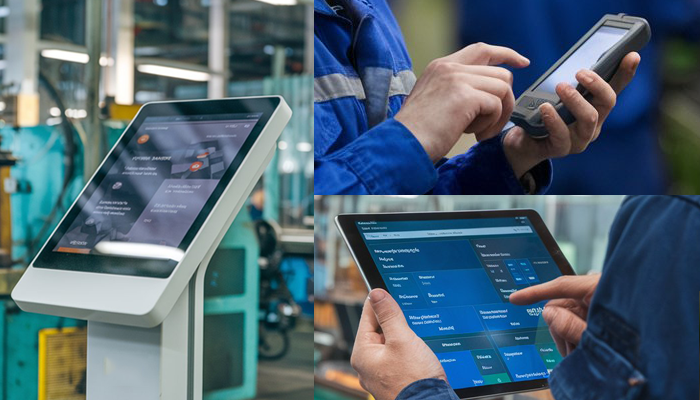
Enter directly
Consult with an Expert
We'll help you find the best plan that fits your company's workforce management requirements.